5700-D Curb & Gutter Machine
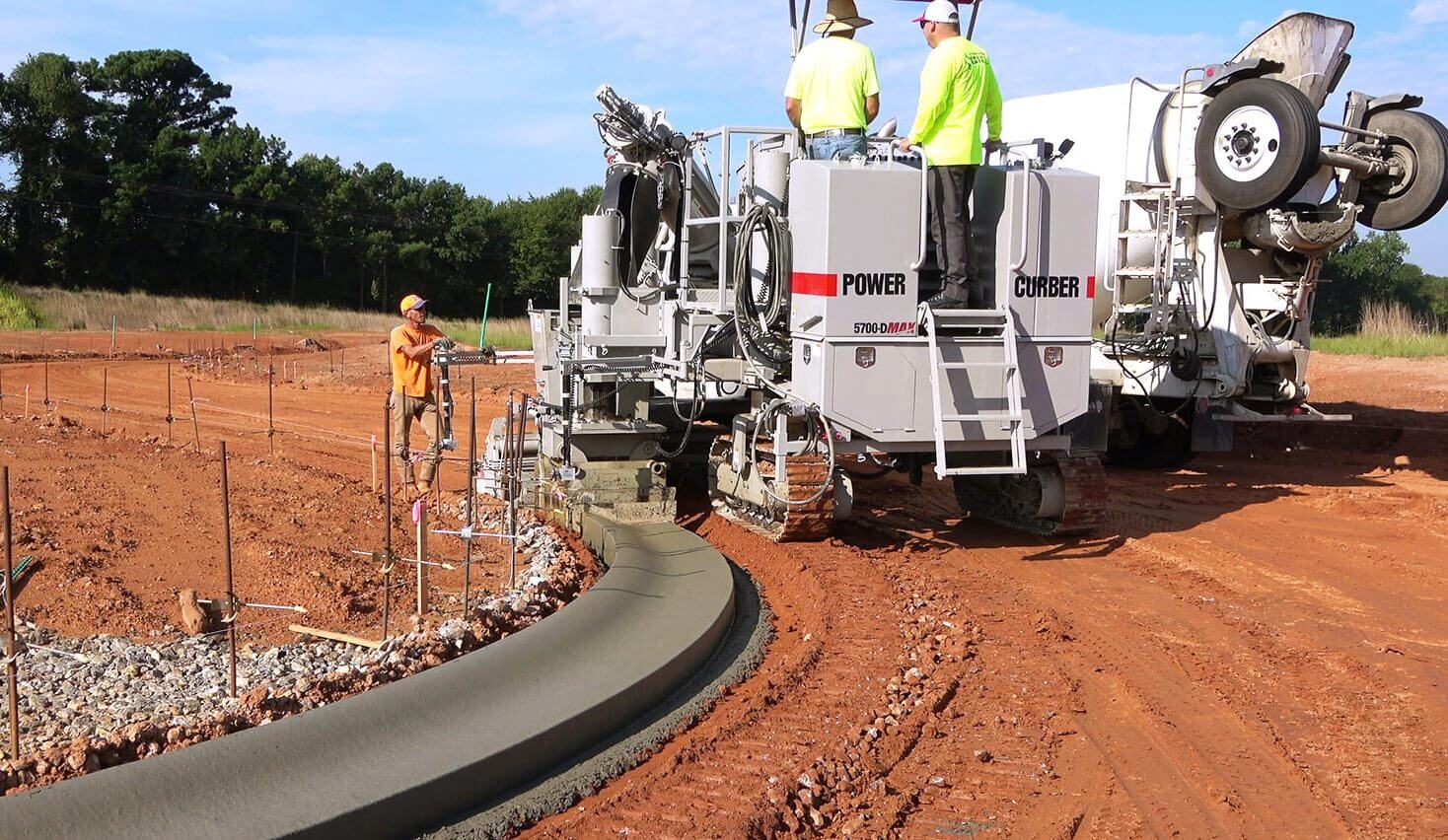
Overview:
The 5700-D is the latest generation of the #1 selling concrete slipform machine in the world. The upgraded Power Curbers SlipSmart Control Solution provides contractors a new level of responsiveness, simplicity and precision. The compact size of the 5700-D makes tight jobs easier to do than ever. The Power Curber 5700-D Curb & Gutter Machine is a “One-Machine Solution” that can easily handle curb & gutter work, highway safety barriers, irrigation ditches, sidewalks and other special applications.
Request QuoteFeatures
SlipSmart Control Solution
The upgraded control system brings a number of improvements:
• Cross-slope controls are smoother, more responsive, and intuitive
• Auto-calibration for the radius steer sensor
• Simplified integration with Topcon, Leica, and Trimble 3-D control systems
• Fine scaling for speed controls
• Standardized display
• Icons for languages other than English
Control Panel Upgrades
We’ve kept much of the control panel the same so the 5700-D will feel familiar while including these improvements:
• “All up” jog switch. With a single switch that raises or lowers all crawler posts simultaneously
• Master vibrator scale knob. In addition to individual vibrator control knobs, the new master control increases or decreases hydraulic flow to all vibrators at once allowing the operator to keep individual vibrators higher or lower relative to each other
• Multiple individual engine gauges are replaced by a single display
• Weather proof switches
• Trimmer “on” light
• Descriptive etched wire labels matching machine schematics
• Cold air dam between engine and console to better regulate control panel temperature and increase operator comfort
• Lightweight aluminum console lid replaces heavy steel lid
• Cupholder
Additional Improvements from Previous Models
• High-pressure water system uses a new pump that can be left “on” without system wear. On-demand high-pressure water will be activated by the wand’s handle.
• New canopy with an overhead lamp available in addition to existing bimini and umbrella choices.
• New door latch style and new doors added to each end of the toolbox. Engine door double latches combined into a single, lower latch
• Auger Conveyor pivot is easier to rotate and the hopper features shovel holders on both sides
• Improved rigidity in mold offset
• Improved low-pressure water system with new pump
• Barrier Mold Lift range increased to 48″ (1220mm)
Compact Design
The 5700-D’s compact design allows operators superior control in tight spots such as cul-de-sacs, islands and parking lot corners. The machine transports at legal width (8’6”/2.59m) and does not require a low-boy.
Visibility
The operator has an excellent view of concrete as it exits the mold, allowing adjustments immediately to minimize handwork behind the machine. The operator also has good visibility of all activity around the machine.
Front Track Steering
To keep things simple, the 5700-D turns a tight radius by steering with the front track only, eliminating coordinating all three tracks together. However, all-crawler steering is available as an option.
Stringless Capable
All-crawler steering equipped machines are ready to work with Topcon, Leica, and Trimble 3-D systems.
Auger Conveyor
After years of building machines with conveyor belts and dealing with their inherent problems like ripping in the middle of a pour and the concrete splatter they cause, Power Curbers introduced the auger conveyor in 1994.
The direct drive, high torque auger:
• Moves volume concrete faster
• Keeps the machine cleaner
• Continues the mixing process of the concrete
• Holds a cubic yard (3/4m3) of concrete which is beneficial in radius and cul-de-sac work
• Conveys concrete regardless of the incline angle of the conveyor
The unique ability of the charge hopper to be positioned in front of the machine, allows a concrete truck to run directly in front of the machine enabling pouring in a single lane of traffic.
Hydraulic Adjustable Offset
The mold mount hydraulically raises, lowers, and side-shifts the mold quickly and easily. With 24” (610mm) of horizontal movement and 16” (406mm) vertical, the mold can be lowered into a trench for rehab curb or for pouring adjacent to existing pavement.
At catch basins, the machine never leaves the stringline and the mold can be positioned within inches of the obstacle, reducing labor-intensive tie-in work.
Trimmer
The stout 42” (1.07m) wide carbide-tooth trimmer handles the toughest of subgrade, minimizing dependence on the grading contractor. Ideally, the trimmer cuts 1-2” (25-50mm) of subgrade but is capable of trimming up to 6” (150mm) in extreme situations.
The trimmer also hydraulically side shifts 80” (2.03m) enabling the ability to trim for a 5’ (1.5m) radius or to move the trimmer under the machine and out of the way when not in use. With 16” (406mm) of hydraulic vertical movement, the trimmer can lift over catch basins and other obstacles.
Options
Climate-Controlled Cab
The fully enclosed, climate-controlled cab allows for powerful air conditioning and heat to keep your operator comfortable without sacrificing visibility.
Pour on the Left and Right Side
The standard setup of the 5700-D is for left side pouring. For highway projects where pouring with traffic is required, the dual side pouring option is available.
Quick Connect Mold Mount
Our most popular optional feature, the patented Quick Connected mold mount, allows mold changes in as little as five minutes. For contractors that change molds often on job sites or go from one application to another, our Quick Connect makes the job simple.
Hydraulic Mold Offset Lock
After using the hydraulic adjustable offset to position the mold, the optional hydraulic mold offset lock enables the operator, at the flip of a switch, to lock the offset rigidly to the machine. Firmly locking the mold to the machine eliminates play in the mold which can affect the finished product. The standard is a manual mechanical lock.
Barrier Mold Lift
At the end of a day’s pour, the hydraulic barrier mold lift allows you to raise the mold up and off the steel cage. With 48″ (1220mm) of stroke in the mold lift and 36” (914mm) of post extension the 5700-D can clear tall steel cages, allowing you to quickly move the machine out of traffic for cleanup and until the next day’s pour.
All-Crawler Steering
In large applications like variable barrier or wall adjacent to an existing structure, our all-crawler steering option is an added benefit. In these large applications, coordinating the steering of all the crawlers can enhance the machine’s performance.
Variable Barrier Molds
Contractors pouring barrier on highways with super-elevations love the ability of the 5700-D to tackle these walls. The 5700-D pours with variable barrier molds typically weighing between 8,000-10,000 lbs. (3630-4535kg) and with up to 24” (610mm) of variability.
Parapet Sensor Mount
Like barrier, the 5700-D pours bridge parapet in a variety of configurations. To help set up for parapet pours, Power Curbers offers a parapet sensor mounting kit and weighted, free-standing stringline stations. Other optional accessories frequently used when pouring barrier include polyurethane track pads and weight pods.
Applications
Curb & Gutter
The 5700-D can handle any curb application with ease. Stand-up curb, also known as header curb or ribbon curb, is common for parking lot islands. Curb & gutter is often used in residential jobs, such as subdivisions. Mold options, such as blockouts and driveway knives, can be added to make your curb jobs even easier.
Radius Work
Pour islands as tight as 2’ (610mm). Our tight radius abilities make the 5700-D ideal for parking lot islands. Eliminating days of hand labor in large retail parking lots, the 5700-D can handle the narrowest of parking lot islands.
For work in areas with less extreme radii the optional hydraulic front grade sensor arm allows the front sensor to stay on line without manual adjustment.
Sidewalk
The 5700-D pours sidewalk or monolithic sidewalk and curb up to 7’ wide (2.1m) in the offset position. Equipping the machine with trimmer extensions, allows the cut to match the sidewalk.
The 5700-D’s adjustable offset allows pouring behind the existing curb and over planter strips. Sidewalk mold options include detachable side plates for pouring adjacent to curb and for secondary sidewalk widths.
Cable Barrier / No- Mow Strips
In some highway applications as an alternative to concrete barrier, cable barrier is used. In these applications the 5700-D contributes in two ways. Using a custom mold in the traditional setup, the machine easily pours a “no-mow” concrete strip which reduces vegetation maintenance under barrier cable.
Before paving the no-mow strip, our post hole digger attachment allows quick and accurate bore holes for anchor posts. Because of the automatic steering and
leveling of a slipform machine, the holes are bored more accurately than with traditional auger equipment. Then, pour over the holes and insert the post sleeves
into the wet concrete.
Center Pour Paving
The 5700-D can be converted into a centerpour paver for wide golf cart and bicycle path paving. Using inserts, the right rear crawler post is moved to allow a paving mold to be installed for widths up to 10’ (3m).
Sectionalized with side plate assemblies and inserts at 4’ (1.5m), 2’ (1m), and 1’ (.5m) widths, the center pour kit gives the flexibility to pour between 4’ (1.5m) and 10’ (3m) wide in 1’ (.5m) increments. The hydraulically adjustable side plates allow the paving depth to vary up to 12” (305mm) thick.
Conversion from the standard offset paving setup requires dropping the auger conveyor and trimmer. Concrete is dumped directly into a hopper at the front of the mold and the spread auger on the paving package spreads the concrete across the hopper.
Ditch Liners
Frequently in mountainous areas, concrete-lined ditches are required for water control. V-ditch molds easily mount to the 5700-D similar to sidewalk molds. Because the trimmer cannot be used in V-ditch applications, preparation of the ditch profile in front of the machine is critical for good results and to avoid wasted concrete. The 5700-D pours ditch liners up to 7’ (2.2m) wide and 2’ (610mm) deep in the offset position.
Slotted Drain
One unique application for the 5700-D is for slotted drain pours. In this application, an inflated polymer-based tube is fed into the front of a custom mold during the pour. The mold is built with a slot from the gutter pan to the cavity created by the tube. After the concrete has cured, the tube is deflated and pulled from the curb leaving a hidden drainage channel.
Canals
The 5700-D is large and versatile enough to make large multi-pass canal projects possible, with custom engineering from the Power Curbers team. Our team can help design massive molds and long conveyors to meet the requirements of any project.
Stadium Risers
The 5700 series machines have poured concrete risers beginning with stadiums used in the 1996 Atlanta Olympics. Since that time, Power Curber machines have poured risers for baseball, football and soccer stadiums worldwide. Typically, custom molds for this application encompass two risers in one pass. Beginning at the bottom of the stadium, risers are poured and the machine works its way up, running on the risers poured the previous day.
Agricultural Applications
From the foundations of large poultry houses to livestock feeding troughs, to beds and flush lanes in cattle barns, the 5700-D adapts to the job with a variety of custom molds.
Tunnel Applications
Tunnel jobs include several perfect slipform opportunities for the 5700-D. Inverts with either a curved or flat profile and rail beds can be poured on the tunnel floor. Walls, walkways, and specialized profiles for housing electrical conduit or other utilities can be poured along the walls. Custom molds can be built to adjust in height and width to handle varying tunnel diameter.
Specifications
Slipform Paving
Curb/Sidewalk Width: Maximum 7’ (2 m) in the offset position or 10’ (3 m) in the center pour position.
Option: Maximum 8’ (2.5 m) wide offset or 12’ (3.65 m) center pour with MAX Package.
Barrier/Parapet Height: Maximum 5’ (1.5 m) tall
Option: Maximum 8’ (2.5 m) tall with MAX Package
Mold: One, up to 32” (813 mm) wide, with quick release interchangeable hopper, is standard.
Engine
Type: Cummins QSB4.5-130C diesel 4-cylinder/4-stroke, turbocharged, Tier 4f emissions compliant. Optional Tier III emissions-compliant engine available where regulations allow.
Power: 130 HP (97 kW) @ 2400 RPM
Service Capacities
Fuel Tank: 66 gallons (250 liters)
Hydraulic Tank: 50 gallons (189 liters)
Controls
Power Cubers SlipSmart Control System: Provides electronic over hydraulic control for grade, forward and reverse steering, and slope.
Features: Adjustment for sensitivity and deadband offering the operator accuracy and feel, without complexity; self diagnostics; and automatic shut-off for sensors that leave the stringline. Networked Digital Control with autoslope, cruise control, 3-D readiness, advanced set-up flexibility, and a large graphic display.
Convenience & Safety: Synchronized ON/OFF for vibrators & crawlers. Five Emergency-Stop switches and a Horn for operator and chute man.
Light Kit: Four post-mounted spot lights and engine enclosure light.
Trimmer
Cutting Width: 42” (1070 mm), up to 78” (1980 mm) with optional extensions. Carbide teeth.
Cutting Head Diameter: 21” (530 mm)
Maximum Trim Depth: 6” (150 mm)
Lateral Shift: 80” (2030 mm) hydraulically
Vertical Shift: 25” (635 mm) – 16” (406 mm) hydraulically, 9” (228 mm) mechanically
Options: Trimmer Extensions in 6” (152 mm), 12” (305 mm), and 24” (610 mm) widths.
Auger Conveyor
Drive: Direct drive with high-torque motor; variable speed and reversible.
Volume: 1 yd3 (0.75 m3) capacity and 0-2 yd3/min (0-1.5 m3/min) rate of movement.
Positioning: Pivots, hydraulically tilts and slides 24” (610 mm). Discharge chute swivels, providing additional flexibility in setup.
Size: 12’ (3.7 m) long and 14” (356 mm) diameter.
Features: Heavy-duty cast flighting with lid for full enclosure.
Vibration
Vibrator Circuits: Six hydraulic circuits with variable speed and independent control
Vibrators: Two, with adjustable mounts
Options: Extra vibrator(s) with hanger and extra vibrator circuits (three)
Hydraulic Adjustable Offset
Lateral Shift: 24” (610 mm) hydraulically with positive mechanical locking.
Vertical Shift: 25” (635 mm); 16” (406 mm) hydraulically, 9” (228 mm) mechanically.
Option: Hydraulic Mold Offset Lock
Water System
Washer: 2,000 psi (138 bar or 13.8 Mpa) high-pressure system with trigger control and adjustable spray nozzle
Tank: Stainless steel with 132 gallons (500 liters) capacity
Options: Low pressure system, Mold misting kit, Charge hopper water kit, Auxiliary water tank (92 gal / 348 liters)
Crawlers & Elevation Posts
Type: Three hydraulically powered crawler tracks with planetary gear reduction
Tracks: 12” (305 mm) wide steel pads
Speed: Travel at 0-110’/min (33.5 m/min), 0-70’/min (21 m/min) with MAX Package. Pouring at 0-50’/min (15 m/min), 0-35’/min (10.5 m/min) with MAX Package.
Minimum Turning Radius: Left at 2’ (610 mm), right at 20’ (6.1 m).
Post Extension: 36” (914 mm) hydraulic cylinders
Straddle Leg: 22” (559 cm) of hydraulic side shift adjustment
Options: Polyurethane track pads and all-crawler steering.
Optional Equipment
Quick Connect Mold Mount: Hydraulically operated
Hydraulic Front Grade Sensor Arm: Operator controlled
Dual Side Pouring: Allows pouring from either the left or right side
Barrier Mold Lift: Hydraulically operated, with 48” (1200 mm) lift, independent of the machine’s post extension.
Weight Pod: 1,980 lbs. (900 kg)
Post Hole Digger: 12” (305 mm) auger diameter. Maximum hole depth is 34” (864 mm). Requires optional Quick Connect Mold Mount.
Center Pour Paving Kit: Available in many widths and configurations.
Stringline Accessories: Stakes, rods, clamps, string, radius materials, winches, etc., available individually or in kits.
Net Weight
Machine: 24,700 lbs (11,200 kg). Weight is approximate and will vary depending on optional accessories and size of mold.
Full Water Tank: Add 1,100 lbs (500 kg)
Full Fuel Tank: Add 480 lbs (215 kg)
Quick Connect: Add 750 lbs (340 kg)
Dual Side Pouring: Add 600 lbs (270 kg)
MAX Package: Add 2,500 lbs (1,135 kg)
Tier III Engine: Subtract 300 lbs. (136 kg)
Transport Dimensions
Length: 20’ (6.1 m).
Add 8” (203 mm) for MAX Package.
Add 16′ (4.9 m) for 28′ Belt Conveyor
Width: 8’ 6” (2.6 m)
Height: 8’1” (2.5 m) without exhaust stack.
Add 5” (127 mm) for MAX Package.
5704-D MAX: Four-Track Slipform Machine
Take the 5700-D to the next level with the 5704-D MAX—our specialized four-track add-on for even larger-scale, complex projects.
From tall highway barriers to parapets, this upgrade delivers enhanced stability, operational visibility and application versatility. It also continues to function as a slipform curb and gutter machine for high-capacity infrastructure work.
Benefits of the 5704-D MAX Addition
The 5704-D MAX slipform machine is designed to handle demanding projects with precision and efficiency, offering the following advantages:
- Increased stability with a fourth post for better balance in extensive applications.
- Low center of gravity and optimal size-to-weight ratio, making it ideal for barrier and parapet work.
- Flexible pouring with a dual-swinging conveyor mount, allowing easy left or right applications.
- Enhanced conveyor options, including a 28′ (8.53m) folding belt for easier transportation, with both belt and auger choices available.
- Hydraulic barrier mold lift with 48″ (1220mm) lift stroke and 36″ (914mm) post extension for quick mold clearance and efficient machine repositioning after each pour.