150 Extruder
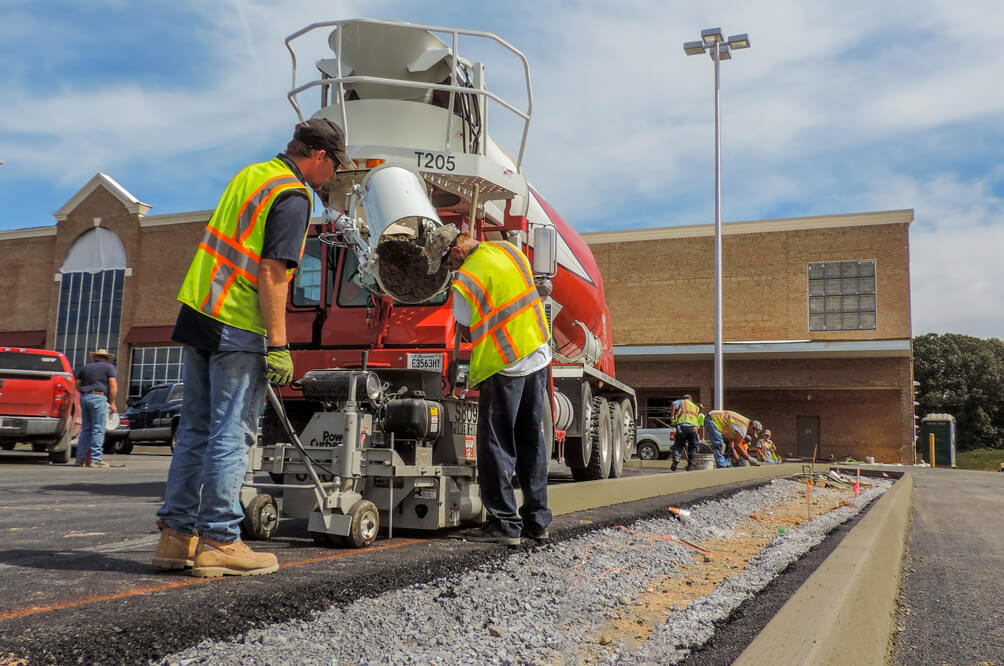
Overview:
Power Curbers pioneered the extruded curb concept in the early 1950s and has been building extruders for over 65 years. For jobs that require less expensive scab-on curb, the 150 extruder is ideal.
The mix is fed into the hopper either directly from the truck chute or by wheelbarrow, and is then forced under pressure through a specially designed mold. The result is a freestanding, structurally sound curb with a smooth finish.
Extruded curb is best placed on top of existing pavement or on a smooth, flat, 95% compacted sub-grade. The 150 extruder can be used for either concrete or asphalt curbs.
See the 150 Extruder in action! Download our 150 Extruder Brochure (PDF)Features
Powerful Engine
Two Honda engine options provide plenty of power to handle hills and curves in parking lots or along streets.
Easy Controls
The 150 features an electric start with the throttle control mounted on the steering handle for easy access from the front of the machine. The steering handle ensures smooth control and easy guidance of the machine from the left- or right-hand position.
Simple Design
The 9 pneumatic tires and 3 lifting jacks make steering and adjusting on the job easy to do. For pouring over an adhesive or for inserting rebar, simply shift the front wheels to the side.
Molds
The 150 can handle molds up to 12” (30 cm) wide and 12” (30 cm) tall. Choose from one of our stock profiles or contact our mold engineers to customize a mold to meet your requirements.
Applications
Trench Curb
In some applications, you may need to extrude curb over a trench. This is done to help secure the concrete curb to the subgrade on which it is being poured. This can be done easily with the 150, as long as the width of the trench is less than the width of the curb mold.
Some operators pour trench curb in one pass, with the trench filling as the curb is formed. Others fill the trench first and then extrude the curb on top of it while the concrete in the trench is still wet. Either method will result in curb that is securely anchored.
Pouring over a trench requires that the forecarriage on the machine be shifted to the side to allow the wheels to run beside the trench.
Pouring Over Pins
The 150 can be used to pour over steel reinforcing pins or dowels embedded in the asphalt subgrade. This type of reinforcement helps anchor scab-on curb onto the asphalt.
This requires modifications to both the machine and mold, and pin height is limited by the height of the mold.
The mold must be designed with a slot to allow the pins to pass through the mold during pouring.
Specifications
Engine
Type: Honda GX630R, 4-cycle air-cooled, electric start
Power: 20.8 hp (15.5 kW) @ 3600 rpm
Optional: Honda GX390, 4-cycle air-cooled, recoil start
Power: 11.7 hp (8.7 kW) @ 3600 rpm
Drivetrain
- Centrifugal clutch with V-belt drive and chain-driven auger
- Single auger drive with compaction chamber
Steering & Elevation
- High-flotation design with 9 pneumatic tires and 3 lifting jacks
Option: Hard rubber wheels in lieu of pneumatic tires
Auger
- 6” hollow-shaft steel auger with 5/8” interior dimension. Can be used for feeding longitudinal rebar through the mold (3/8” [10 mm] maximum rebar diameter).
Options: 5” hollow-shaft steel auger, for small profile molds; 6” cast auger (solid shaft). Spare augers available in all sizes.
Mold
- 1 curb mold included
Option: Extra molds available
Paving Specifications
Paving Speed (Maximum):
20.8 hp (15.5 kW): 25 feet/minute (7.6 m/min)
11.7 hp (8.7 kW): 15 feet/minute (4.6 m/min)
Curb Width: 12” (30 cm) maximum
Curb Height: 12” (30 cm) maximum
Clearance: Within 1” (2.5 cm) of obstructions
Radius (minimum): 24” (60 cm)
Hopper Capacity
- 4 cubic feet (0.1 cubic meters)
Dimensions
- Length: 6’ 4.5” (1.94 m) with steering handle upright (8’ 5” [2.57 m] with steering handle in the brake position)
- Width: 30” (76 cm)
- Height: 32.5” (83 cm)
- Weight:
20.8 hp (15.5 kW): 950 lb (431 kg)
11.7 hp (8.7 kW): 800 lb (363 kg)
Other Optional Equipment
Dual-side Pouring: Second mold, auger, housing, compaction chamber, and shaft for left- or right-side extrusion
Under Guardrail Pouring: Offsets the mold, auger housing, and compaction chamber to pour underneath an existing guardrail. Consult factory for specific applications.